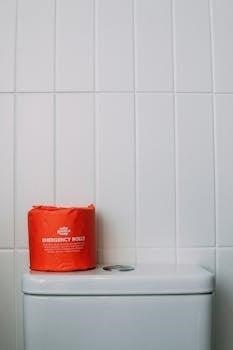
AS/NZS 1554 is a crucial joint standard that provides comprehensive guidelines for welding structural steel in Australia and New Zealand, covering residential, commercial, and industrial welding projects to ensure consistent quality․
Overview of the Standard
The AS/NZS 1554 standard, particularly part 1, is a pivotal document specifying requirements for welding steel structures, encompassing various forms like plates, sheets, sections, hollow and built-up profiles, castings and forgings․ This standard emphasizes the importance of adherence to quality procedures for all welding activities, ensuring structural integrity in diverse applications․ It serves as the benchmark for structural steel welding in Australia and New Zealand․ It was developed by a Joint Technical Committee, emphasizing collaborative standard setting processes․ The standard includes requirements for welding reinforcing steel, connections, inserts, anchors, and prefabricated components used in concrete structures․ It is a comprehensive guide for welding procedures, welder qualifications and quality control․ The standard ensures that welding practices meet the required safety and performance levels across different projects, providing detailed guidance on weld size and placement, as well as necessary training for welding personnel․
Scope and Application of AS/NZS 1554․1
AS/NZS 1554․1 applies to the welding of steel structures using plates, sheets, sections, and hollow profiles, including built-up components, castings, and forgings in construction projects․
Welding of Steel Structures
AS/NZS 1554․1 specifically addresses the welding of steel structures, encompassing a broad spectrum of applications from building homes to large commercial and industrial facilities․ This standard provides detailed requirements for welding steel components, including plates, sheets, sections, and hollow profiles, as well as built-up sections, castings, and forgings․ It is designed to ensure that all welding activities meet stringent quality and safety standards․ The standard’s scope extends to both fabrication in workshops and on-site welding, demanding consistent adherence to its guidelines to maintain structural integrity․ Its provisions are critical for ensuring the reliability of welded steel structures across various sectors, mandating compliance with specified weld sizes, placements, and the necessary training for welding personnel․ The aim is to ensure the structural integrity and durability of steel constructions in all applications․
Materials Covered
The AS/NZS 1554․1 standard is applicable to a wide range of steel materials used in structural applications․ This includes various forms such as steel plates, sheets, and sections, encompassing both standard and hollow profiles․ It extends to built-up sections which are common in larger structural components․ The standard also covers castings and forgings, ensuring that welding procedures are appropriate for different manufacturing processes․ Moreover, AS/NZS 1554․1 addresses the welding of reinforcing steel when it is used in concrete structures, aligning with other standards like AS 3600 and NZS 3101․1․ It is important to note that the standard is applicable for welding any non-pressure stainless steel equipment and connection devices, inserts, anchors, and prefabricated details․ The materials are specified to ensure that the correct procedures are followed for welding, based on their composition and intended use in structural contexts․
Key Requirements of AS/NZS 1554․1
This standard outlines critical requirements for welding procedures, welder qualifications, and quality control, which are fundamental to ensuring the integrity of welded structures according to AS/NZS 1554․1;
Welding Procedures
AS/NZS 1554․1 meticulously details the requirements for welding procedures, ensuring that all welds meet specific standards for strength and durability․ These procedures are essential to guarantee the structural integrity of steel fabrications․ The standard provides guidelines on weld size and placement, ensuring that welds are effective in resisting imposed loads․ It covers various aspects, including the selection of appropriate welding processes, materials, and techniques․ Furthermore, it emphasizes the importance of proper joint preparation, including cleaning and fit-up․ The standard also addresses preheating and interpass temperature control to minimize the risk of cracking and distortion․ Additionally, it outlines the need for procedure qualification records to demonstrate that the selected welding parameters produce acceptable welds․ It requires welders to adhere to documented procedures, ensuring consistent and reliable results on every weld․ This meticulous approach ensures that all welding is carried out to a high standard, thus maintaining the safety and reliability of welded steel structures, reducing the risks of failure and ensuring long term performance․
Welder Qualifications
AS/NZS 1554 mandates that welders must be adequately qualified to perform welding on structural steel․ This requirement ensures that individuals undertaking welding tasks possess the necessary skills and knowledge to produce sound and reliable welds․ The standard references ISO 9606 for welder qualification testing, which involves practical assessment of a welder’s ability to produce welds that meet specified requirements․ Welders must demonstrate competency in specific welding processes, positions, and material types․ Qualification testing involves creating test welds that are then subjected to visual inspection and potentially non-destructive testing to verify the weld quality․ The scope of a welder’s qualification is limited to the processes and positions they are tested in․ Regular requalification is often required to ensure welders maintain their skills․ By ensuring welders are properly qualified, AS/NZS 1554 helps to maintain a high standard of welding practice, reducing the risk of weld defects and structural failures․ This emphasis on welder competency is a vital aspect of maintaining the integrity and safety of welded structures․
Quality Control and Inspection
AS/NZS 1554 places a strong emphasis on quality control and inspection throughout the welding process․ This ensures that the final welded product meets the required standards and is fit for its intended purpose․ The standard mandates that all welding work must be subjected to some level of inspection, regardless of whether it is fabricated in a factory or on-site․ Inspection activities include visual examination of welds to identify any surface defects, and where necessary, non-destructive testing methods are used to detect internal flaws․ These tests can include ultrasonic testing, magnetic particle inspection, and dye penetrant testing․ Quality control procedures are implemented to ensure that welding processes are performed correctly, that materials are stored and handled appropriately and that welder performance is consistently evaluated and maintained․ The type and extent of inspection required are determined by the criticality of the weld and the application of the fabricated structure․ Maintaining proper quality control and inspection practices is essential for ensuring the integrity and durability of welded structures, minimizing the risk of failures, and ultimately ensuring the safety of those utilizing the structures․
Related Standards and Documents
AS/NZS 1554 references several related standards and documents such as AS 1674․1 for fire precautions, AS 1101․3 for welding symbols, and ISO 9606 for welder qualifications․
AS 1674․1-1997 Fire Precautions
The AS 1674․1-1997 standard, titled “Safety in welding and allied processes, Part 1⁚ Fire precautions,” is a crucial document that outlines the necessary safety measures to prevent fires during welding operations․ It is a cited reference within the AS/NZS 1554 standard, emphasizing the importance of fire safety in welding․ This standard provides specific guidelines on fire prevention, including the safe handling of welding equipment, the proper storage of flammable materials, and the implementation of appropriate fire extinguishing measures․ It also details the responsibilities of personnel involved in welding activities concerning fire safety․ Compliance with AS 1674․1-1997 is essential for ensuring a safe working environment and minimizing the risk of fire incidents during welding projects, thereby protecting both personnel and property․ It is an integral part of the broader safety framework associated with welding processes, working in conjunction with AS/NZS 1554 to promote safe and effective practices․ These combined standards contribute to a comprehensive approach to welding, addressing both technical requirements and safety concerns․
AS 1101․3-2005 Welding Symbols
The AS 1101․3-2005 standard, specifically “Graphical symbols for general engineering, Part 3⁚ Welding and non-destructive testing,” is an essential reference cited within the AS/NZS 1554 standard․ This standard provides a comprehensive system of graphical symbols used to represent welding and non-destructive testing information on engineering drawings․ It ensures a consistent and clear method for communicating welding requirements and specifications․ By using standardized symbols, engineers, welders, and inspectors can effectively interpret and implement welding procedures․ The standard covers a wide range of welding-related symbols, including those for weld types, joint configurations, and non-destructive testing methods․ The use of these symbols facilitates accurate communication, reduces errors in fabrication, and ensures that welding is performed according to design specifications․ This promotes clarity in technical documentation, making the process more efficient and less prone to misinterpretations․ Understanding and utilizing the symbols from AS 1101․3-2005 is a key component of competent welding practice, aligning with the broader requirements of AS/NZS 1554․
ISO 9606 Welder Qualification
The ISO 9606 standard, which focuses on the qualification testing of welders for fusion welding, is closely linked with the AS/NZS 1554 requirements for ensuring welding quality․ This international standard sets out the necessary procedures for qualifying welders, establishing the competency and skill levels of welding personnel․ It specifies the testing methods, acceptance criteria, and certification processes for welders working with various welding processes and materials․ The standard serves as a benchmark for assessing a welder’s ability to produce welds meeting specified quality and safety requirements․ By adhering to ISO 9606, companies can ensure that their welders are qualified to perform their tasks effectively, reducing the risk of errors and defects in their welded structures․ Australian fabrication often complies with ISO 9606 standards for welder qualifications, demonstrating commitment to international best practices and quality in welding․ The use of this standard ensures consistency and reliability across different welding operations․ This helps in maintaining standards for welder training, and competency assessment․
AS/NZS 1554 and Fabrication Compliance
All Australian fabrication adheres to AS/NZS 1554 for structural steel welding, ensuring that welding practices meet the specified requirements for quality, safety, and structural integrity during the fabrication process․
Australian Fabrication Standards
Australian fabrication standards, primarily governed by AS/NZS 1554, mandate that all structural steel welding aligns with the rigorous guidelines outlined within this standard․ This ensures that welding procedures, welder qualifications, and quality control measures are consistently implemented across all projects․ The standard encompasses a wide range of applications, from residential buildings to large-scale commercial and industrial structures․ Compliance with AS/NZS 1554 is not just a recommendation but a necessary requirement for any fabrication work involving steel, ensuring structural integrity and safety․ The standards also emphasize the importance of using appropriate materials and techniques, and they define the necessary inspection and testing protocols to verify the quality of the welds․ Furthermore, these standards often reference other relevant documents, such as ISO 9606 for welder qualification, creating a cohesive framework for fabrication excellence․
Fatigue Loading and AS/NZS 1554․5
AS/NZS 1554․5 specifically addresses the welding of steel structures that are subject to high levels of fatigue loading, providing crucial guidance for such applications, which is essential for safety․
Welding Structures Subject to Fatigue
Welding structures that experience fatigue loading requires meticulous attention to detail, as these structures are repeatedly subjected to stress, which can lead to cracking and failure․ AS/NZS 1554․5 offers specific guidelines to mitigate these risks, focusing on appropriate welding procedures, material selection, and weld design to enhance the structure’s durability․ The standard acknowledges that fatigue is a critical consideration in structural integrity, particularly in scenarios involving dynamic loads or cyclic stresses․ By adhering to the recommendations in AS/NZS 1554․5, engineers and fabricators can create welded joints that are more resistant to fatigue cracking, thus prolonging the service life of structures and ensuring safety․ This part of the standard helps ensure that structures can withstand repeated loading without compromising their overall performance․ Proper implementation of these standards is vital for infrastructure and equipment exposed to high fatigue conditions․